碳素铬铁是冶炼不锈钢、轴承钢最重要的合金添加荆,碳索铬铁在冶炼过程中,由于炉渣熔点高、粘度大,在出铁时技术上很难使渣铁彻底分离,因而在渣中难免要混入3~5%的碳素铬铁.这些炉渣冷却后,很难用人工的方法分离,达剑划收利用的目的.以往传统的方法是将其抛弃,这样做既占用了大量的土地,浪费了宝贵的铬矿资源和能源,也在不同程度下污染了环境。1992年我厂碳素铬铁产量逾1.5万吨,年排渣量约1.6万吨。
为了达到既能回收渣中铬铁,提高铬元素的回收率,又能综合利用铬铁渣的义重目的,我厂在1992年用小到三个月的时呵,自行设计、组织施工建设了一条采用跳汰机回收碳素铬铁的生产线。
1 生产工艺流程和主要技术指标
1.1生产工艺流程(见图1)
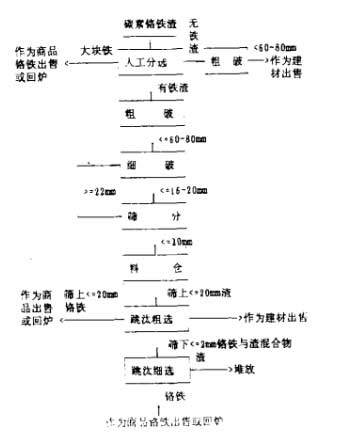
1.2主要披术经济掘标
年处理铬铁渣能力:20000t
年回收铬铁:700t(按渣中含铬铁5%.回收率70%计)
年生产建筑材料:块度60-80mm 15000t
块度<20mm 4000t 装机容量:120kw产值150万元/年
经济效益。利税总和100万元/年
跳汰生产工流程图
2 设备选型
整条生产线主要由破碎、筛分、跳汰分选、输送,料仓、给料等设备组成,共计有18台套).生产线上机械化程度较高.因而生产定员较少,工人劳动强度较低.
2.1 破碎设备
破碎设备选用的是一台粗碎设备和两台细碎设备,使生产能力配套。
粗碎设备选用的是PE400型颚式破碎机,该设备最大给料粒度为<350mm.排料调整范围为40-100mm.生产能力为25-64吨/小时。
为丁节约工程投资和加快工程进度,细碎设备利用两台旧的PE250型破碎机.由于该设备排料口调整范围为20-80mm.虽经改进设备肘板,碎后的铬铁渣粒度仍过大,经滚筒筛筛分后返回料太多,这样既浪费了能源,又不能满足生产能力的需要。故可认为,该生产线选用该型号破碎机是不适宜的。如选用另一种细碎型俪式破碎机,其最大给料粒度120mm,排料口调整范围10-40mm.生产能力为15-35吨/小时,效果会更好。
2.2 筛分设备
筛分设备选用的是自行设计制造的滚筒筛。滚筒筛规格为960×3000.筛孔直径为20.筛孔敦约为1.1万个,滚筒筛转速为15转/分.该设备生产能力为3吨/时,滚筒筛与自定中心振动筛相比,具有设备坚固耐用、维护方便、小需经常更换筛网、生产能力大等优点,经长期使用,证明效果较好。
2.3 跳汰设备
跳汰机是该生产线上的关键设备.该生产线选用了两台LTS300×450型双斗隔膜跳汰机.根据需要我们对设备作了多处修改,该设备处理铬渣能力为2吨/时.
3 生产实践几个问题的探讨
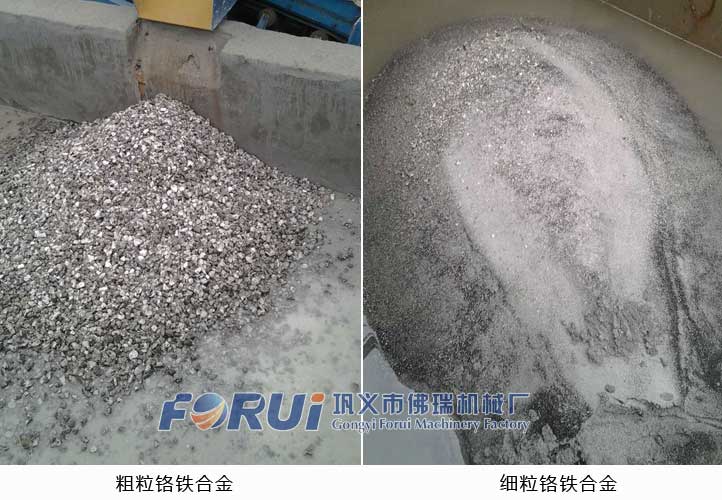
3.1 严格把好人工分选关
碳素铬铁在生产过程中,出铁时各个部位渣中所夹带的铬铁含量是不同的。铁水包底、淌橹和渣包底部,渣中央带铬铁含量较高,这种渣的数量相对较少,而它正是跳汰的主要对象.渣包中卜部的渣,数量很大,约占全部渣量的7D%以上,但铬铁含量很低,用于跳汰分选很不经济,应直接破碎成一定块度作为建材出售。碳索铬铁渣在从生产车问用汽车运输到跳汰生产线的过程中,各种渣是混合在一起的,因此,必须用人工分选的方法,将有铁渣和无铁渣区分开,分别处理.这样做,不仅可以大大减轻跳汰生产线上大部分设备的工作负荷,节约能源,减少设备磨损,达到事半功倍的目的.而且,在分选的过程中,也可以将铁块、螺栓等有在夹物挑选出来,从而保证破碎机的安全,
3.2 确定合适的给矿粒度
在设计阶段.我们依据有关资料介绍,选定滚筒筛孔限直径为16mm.经过一段时间生产实践,发现孔眼直径小,破碎成品率低,经常造成跳汰机无料可跳,所以,投产初期,产量很低。针对上述问题,我们将滚筒筛的孔眼直径扩大为20mm.改进后,改进后,破碎成品率明显提高.目前,跳汰机单机日产可达J吨,渣铁分离的效果较好.
3.3 选择合理的跳渣工作制度
通过摸索试验,选择合理的跳汰工作制度是关系到跳汰回收铬铁产量高低,渣铁分离效果好坏的主要因素.
我厂所选用的跳汰工作制度如下:
给料粒度:≤20mm
给料速度:2t/h
冲程:17. 5mm
冲次:322欢/分
工作水堆:0.2MPa
4 生产实践与结论
我厂自行设计、建设的这条生产线,自1992年10月投产以来,经过9个多月的生产运行,巳处理了铬铁渣1万多吨,从渣中回收铬铁约400吨,相当于节电140万kw.h。可以预计,这条生产线今年所获得的效益有不仅可以偿还当初建设这条生产线的全部工程贷款,而且,还将有部分盈余,经济效益十分可观。实践证明,采用跳汰法从碳素铬铁渣中回收铬铁的生产工艺是守全可行的。它具有生产工艺简单、工程投资少、建设速度快、操作维修方便、渣铁分离效果好、经济效益和社会效益十分显著的优点.今后,除了继续改进,完善现有生产工艺,提高回收率以外,应加强对铬铁渣的回收技术推广应用和研究,真正使废渣变废为宝,届时,该生产线所发挥的经济效益将会更加显著。(作为商品铬铁出售或回炉)